Innovation Breakthroughs and Value Creation
Real-time and flexible problem-solving for customers, providing
customers with the most advanced processes for future use.
Strategic Objectives | 2023 Goal | 2023 Achievements | 2024 Goal |
---|---|---|---|
Strengthen research and development capabilities and build a patent map |
|
|
|
Key Products
Mask Carrier Solutions
After decades of effort, Gudeng developed the world's second and Asia's first EUV Pod, which
utilizes top-notch CNC technology, composite material injection technology, and super mirror
processing to achieve an exterior design at an exceptionally high level. Gudeng holds a
market share of over 80% globally and possesses seven exclusive patents. Among them, the
2009 invention patent for "Extreme Ultraviolet Photomask Container – Moat" is the world's
first and enhances exposure efficiency, reduces rework, and improves process yield, becoming
a new milestone for the technology transfer in semiconductor processes.
Gudeng's ability to maintain a leading position in advanced EUV technology mainly stems from its collaborative development of custom products with customers. Through thorough discussions with customers during the initial design phase to meet their needs, Gudeng integrates upstream and downstream customers and suppliers to create a flexible and efficient service platform. Finally, Gudeng introduced high-quality equipment and automation devices to improve production efficiency and actively recruited excellent research and development talents to continue expanding research and development capabilities.
EUV POD Development Progress in the Past Decade:
- In 2019, the new generation of EUV POD-G/GP Type was certified by ASML.
- In 2020, we successfully contributed to enhancing our 7-nanometer process yield and improving production capacity, earning a letter of appreciation from TSMC.
- In 2021, we continued research and development of the new generation of EUV POD.
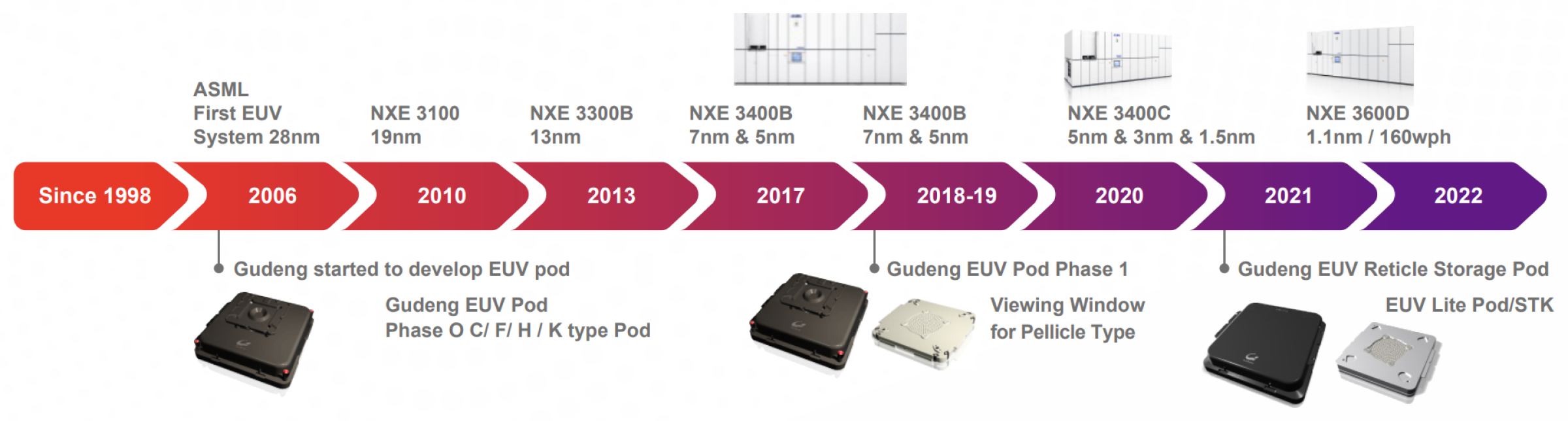
Why did the EUV-Pod have a chance to succeed?
Collaborative Creation
Regular meetings with key customers and factories
for ten continuous years.
High Execution Power
Using the strongest execution power to meet
customers' most urgent demands.
Integrated Manufacturing
Providing highly flexible production capacity to
respond to customers' temporary high demand.
Through CEO's real-time
decision-making, customers' needs are met and solved promptly.
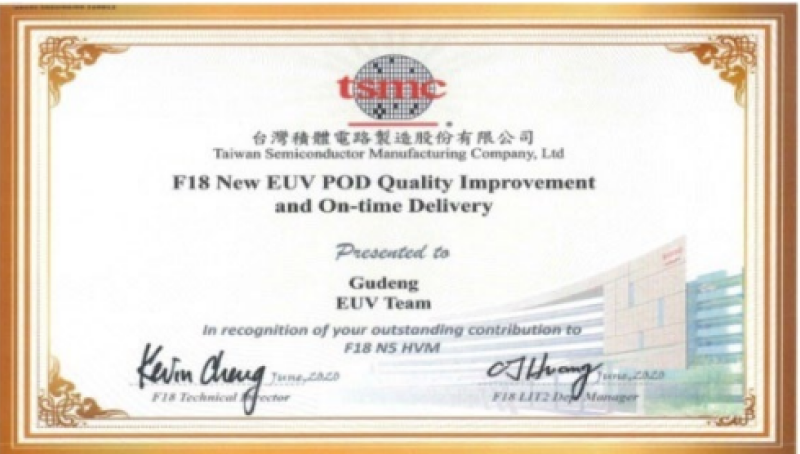
Through co-creation of Co-Creation, effectively help improve the yield rate, and get a certificate of appreciation.
Wafer Carrier Solution
Front Opening Unified Pod (FOUP) is a container used in semiconductor processes to protect,
transport, and store wafers, effectively reducing the risk of wafer contamination by
particles. It is a critical production tool in advanced 12-inch wafer fabs. Gudeng Precision
has invested years of research and development in FOUP and became the only Taiwanese
manufacturer to join SEMI's efforts in formulating the 450mm FOUP specification in 2011. We
have successfully increased customer production yield and efficiency and gradually captured
domestic and international market share. With the global market size of FOUP and FOSB
reaching 724.6 million US dollars, it is expected to reach 1.15 billion US dollars in 2029,
with a 7.05% compound annual growth rate in the past five years, providing robust
operational momentum and stable revenue growth.
In 2023, we collaborated with local supply chains to develop low outgassing materials,
significantly reducing the release of organic compounds and improving product
cleanliness.
Development Progress
Development Progress
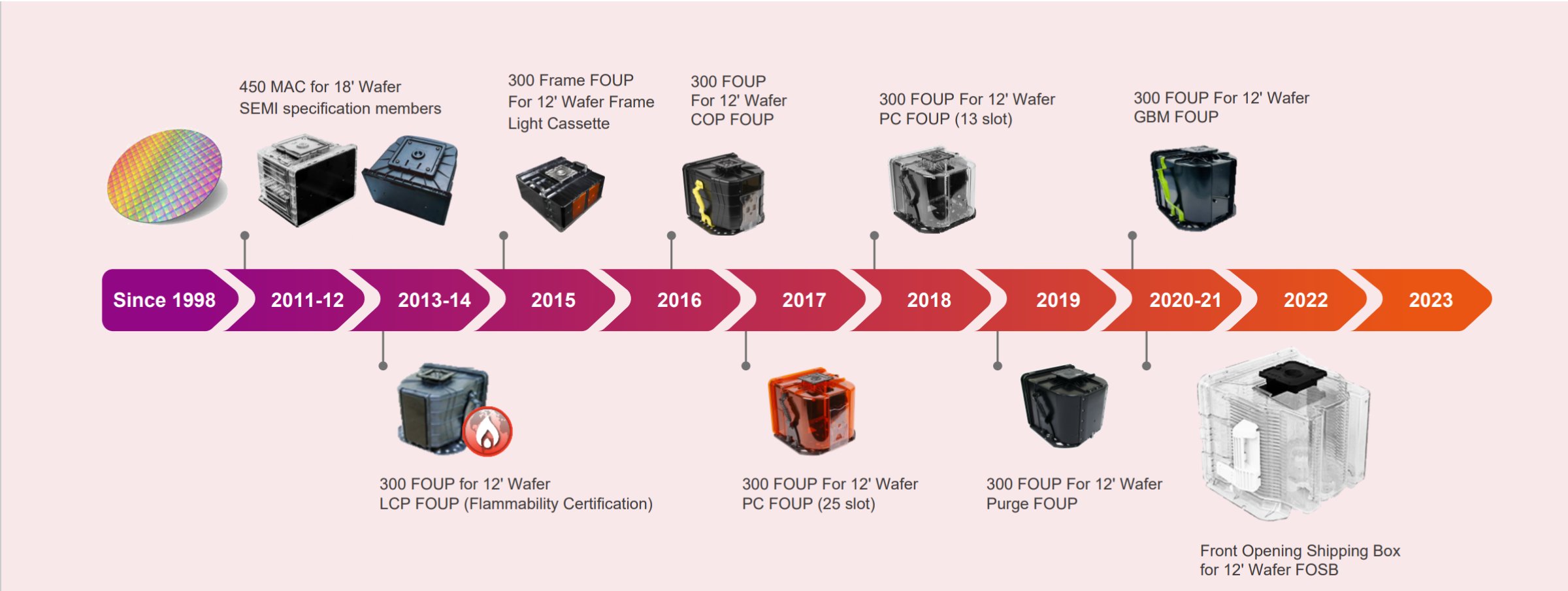
R&D and Innovation Strategy
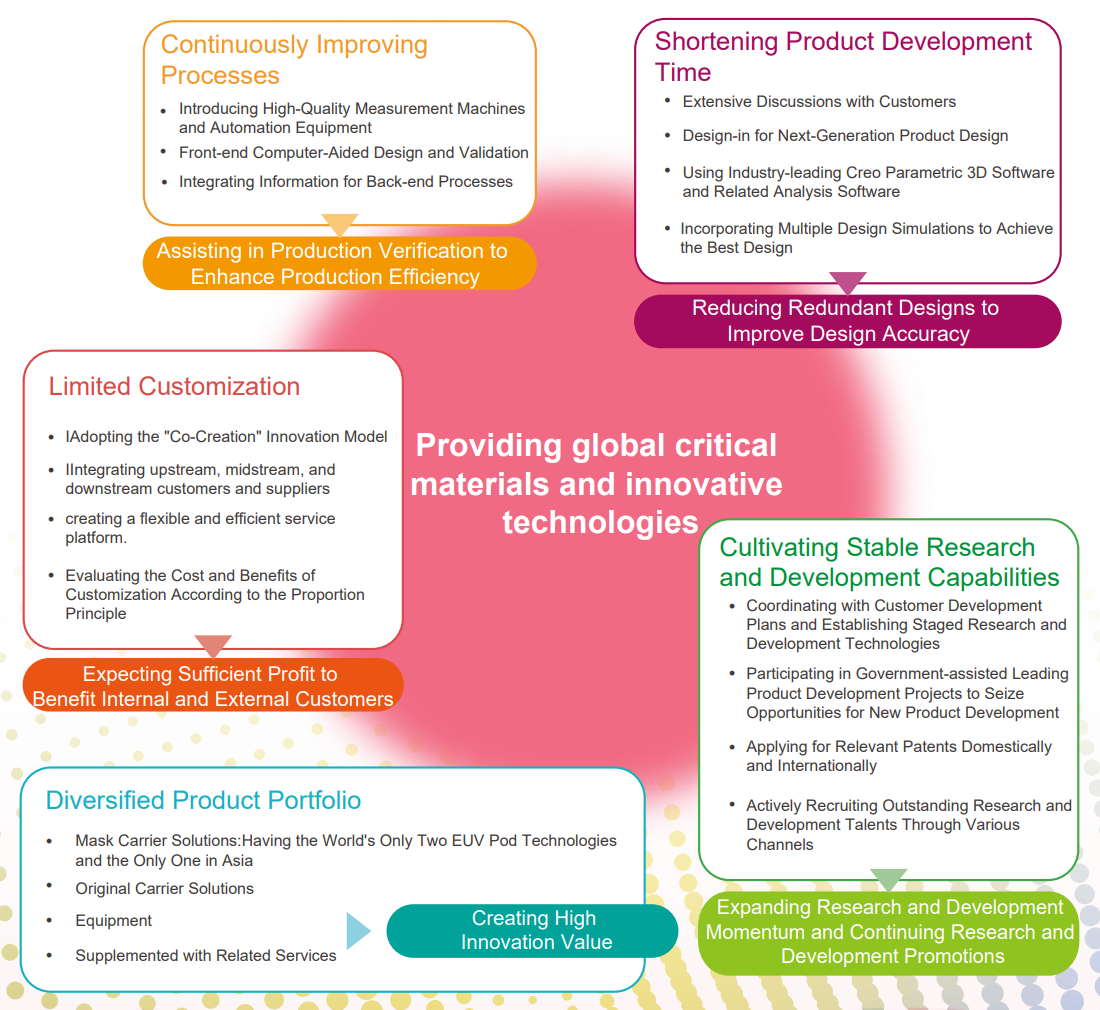
Research and Development Innovation Process
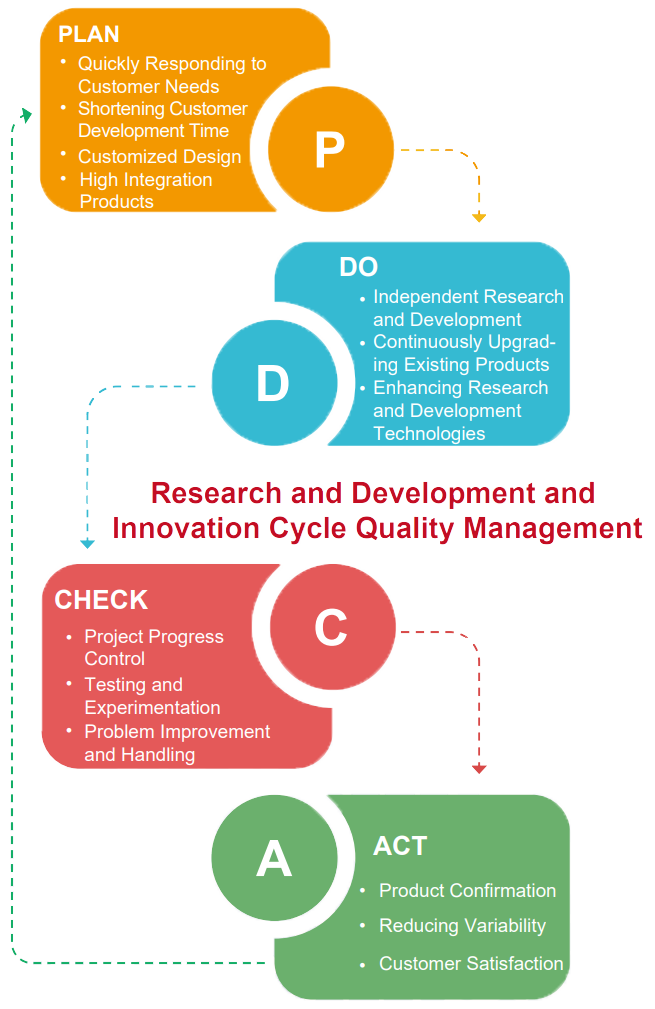
Investment in Research and Development Innovation Activities
Since its establishment, Gudeng Precision has been aware that investing in research and
development is a long-term journey that requires step-by-step progress to bear fruit.
Therefore, over the years, the company has invested significant funds to stimulate research
and development momentum.
The cumulative research and development expenses disclosed in the financial report up to 2021 have reached 1.2 billion New Taiwan Dollars, and the expenditure in 2023 has exceeded the average, reaching a record-breaking 222 million. Strict case review and evaluation are conducted to understand the next-generation semiconductor development trends, determine strategies, present market differentiation, and achieve multiple breakthroughs in 2023's group revenue. In addition to earning 660 million in new product revenue from 2020 to 2023, the total revenue also reached a historical high in each quarter.
Year | R&D Expenses | Revenue | R&D Expense Proportion |
---|---|---|---|
2020 | 84,189 | 1,213,810 | 7% |
2021 | 120,552 | 1,430,164 | 8% |
2022 | 146,421 | 1,994,676 | 7% |
2023 | 222,723 | 3,159,978 | 7% |
Unit: thousand NTD dollars
Cumulative Patents
In 2009, we introduced Taiwan's intellectual property management regulations, and in 2019,
we obtained TIPS A-level certification. In 2023, we actively planned our intellectual
property map and strengthened the establishment of our patent system and defense
capabilities, demonstrating our emphasis on intellectual property and continuously expanding
and establishing a high-tech industry position that other large companies cannot win solely
on scale.
To date, we have accumulated 558 patents, with 191 more in continuous application. In 2023, 57 patents were granted.
Year | Cumulative Patents |
---|---|
2020 | 431 |
2021 | 456 |
2022 | 511 |
2023 | 558 |

Research System Education and Training
In 2022, a curriculum training system was developed for research and development personnel,
incorporating digital learning fields such as SEMI specifications, aerospace product
assembly standards, product cleaning, product development, and project acceptance and
transfer.A total of 17 courses were offered, with 277 participants and a total training time of 192.5 hours.
R&D Personnel | Doctoral | Master's | Bachelor's | Full-time | Total |
---|---|---|---|---|---|
2022 | 1 | 17 | 18 | 4 | 40 |
2023 | 1 | 25 | 26 | 3 | 55 |
Industry-Academia Collaboration
To strengthen the proactive research knowledge management database, Gudeng Precision
actively participates in the leading domestic industrial bureau's new product program and
strives to secure opportunities for technology transfer or joint development abroad,
stimulating research and development and technological upgrading. In addition to passing
five government projects from 2020 to 2023 (with subsidies totaling 38.1 million), including
projects such as automated cleaning systems for photomask carriers, which increased
operating efficiency by at least 1.75 times, the estimated benefits in the next three years
could reach 875 million. Not only leading in technological fields, but Gudeng Precision also
delivered several technical forum speeches, sharing the impact and changes of EUV technology
on future technology.
Quality Technology, Intelligent Manufacturing, Digital Transformation
Strategic Objectives | 2023 Objectives | 2023 Achievements | 2024 Goal |
---|---|---|---|
Quality Management | Implement DMAIC projects, combining lean production with Six Sigma. | A total of 19 colleagues obtained Green Belt certification through training and practice, improving production issues such as product design, line efficiency, and product yield, resulting in total benefits of NT$17 million. | Enhance the management system, ensuring the accuracy of SPC basic data Objective >= 100% Pass the aerospace NADCAP certification. |
Intelligent Process | Establish an AI project team, introduce intelligent manufacturing management processes, and achieve NT$36 million in process improvement benefits. | Complete 11 improvements through cross-unit collaboration, resulting in benefits of NT$36,005,745. | Establish a robotic process automation (RPA) project team to optimize daily operations' efficiency. |
Gudeng Precision's management team attaches great importance to quality issues, and comprehensively manages all stakeholders by developing a quality system blueprint. The company actively implements the quality concept in all management activities. Mobilizes all staff based on daily item management principles, and implements PDCA to achieve the best management results in terms of quality, quantity, and cost. Starting with quality, efficiency is achieved. Good quality starts from the heart.
Quality Enhancement Project – DMAIC Competition
In 2021, the DMAIC project was initiated, conducted by a 30-member team trained and
implemented by SGS Taiwan Inspection Technology Company's 6 Sigma GB. Analytical tools were
introduced, and statistical analysis methods were applied to inspection methods and Design
of Experiments (DOE) to determine the optimal parameter conditions for optimizing output and
transferring results to operational standards. In 2022, a quality management competition was
held to improve efficiency, and the best team received an award.
In 2022, 19 students obtained DMAIC Green Belt certification, and during the project period, the benefit amount reached NT$17.07 million.

Improved cross-departmental collaboration and received public recognition
Supplier Quality Management
Gudeng proposes the "eCOA" (Electronic Certificate of Analysis)
policy, where suppliers provide critical shipment inspection parameters in
electronic data format, referencing Gudeng's eCOA format. This eCOA format is internally
encoded and linked to Gudeng's SPC system, and after data uploading, it becomes a key
parameter for Incoming Quality Control (IQC). The statistical and cumulative data analysis
allows for quality control and connection with Gudeng's advanced intelligent manufacturing
process, extending the core spirit of quality management to suppliers.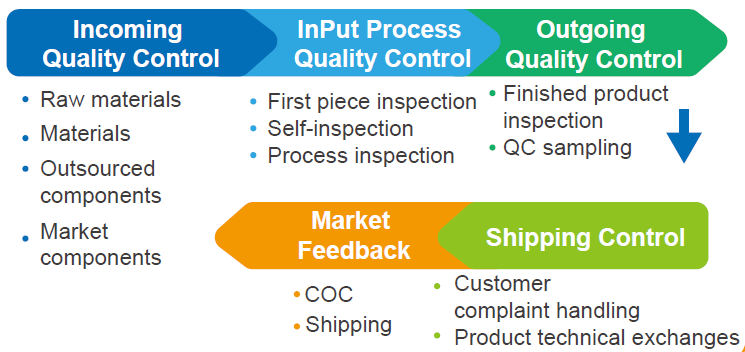
Smart Manufacturing
In 2007, Gudeng Precision had revenue of only slightly over NT$300 million. Fully aware of
the mission of serving world-class semiconductor manufacturers and the significance of
information technology to organizational entities, the company decisively invested in
implementing an Enterprise Resource Planning (ERP) system following semiconductor plant
standards, namely SAP, and collaborated with the IT team to plan the information system
blueprint.
In 2022, the AI Smart Manufacturing Development Committee was established, organizing cross-departmental meetings weekly to formulate four major strategic axes, continuing to drive digital transformation, and introducing Advanced Planning and Scheduling (APS) and Big Data AI to replace human decision-making. The aim is to accurately predict delivery dates, visualize production capacity status, dynamically allocate production resources, and improve planning efficiency, enabling real-time access to various operational and production-related information to facilitate decision-making and planning.
During the digital transformation stage, Gudeng gradually develops new business
models by introducing advanced automated intelligent manufacturing from the
semiconductor industry into traditional factories, becoming a leader in intelligent
factory manufacturing.
The journey towards smart manufacturing is still long, but we have already taken the first steps.
The journey towards smart manufacturing is still long, but we have already taken the first steps.
AI Computation for Injection
Parameters
- One-click calculation of injection parameters to shorten trial mold time and frequency and enhance trial mold efficiency.
- Digital preservation of manufacturing experiences.
- One-click parameter recall on the industrial control platform.
Smart Scheduling with APS
- AI-driven scheduling replacing human decision-making.
- Real-time calculation of Key Performance Indicators to grasp production status.
- Increasing production flexibility through system insertions and material planning scenarios.
- Visualizing production capacity status and dynamically allocating production resources.
Robot Process Automation
(RPA)
- Releasing human labor from low-value tasks.
- Improving operation immediacy.
- Timely processing without omissions.
- Enhancing efficiency through batch processing.
- Reducing error rates.
Smart Manufacturing Big Data
Integrating crucial information on production
manufacturing and business operations,
presenting financial, sales, manufacturing,
material, and other key topics on an interactive
platform, serving as a decision-making and
meeting platform, consolidating consensus and
improving execution.
Four Major Strategic Axes
Introduction of Smart Factory
Intelligent
Cleaning
Intelligent
Inspection
Intelligent Packaging
Information
Intelligence
To continuously improve the efficiency of management mechanisms, we employ technology-driven
systems such as SPC and MSA. Additionally, we collaborate with Chung Yuan Christian
University for development and research, including literature exploration, project
execution, and system implementation. We have also devised AIQ smart quality self-adjusting
control parameters, utilizing AI assembly supervision systems, appearance inspection
machines, AI assistance, and AOI to achieve our goal of "Lean Production, Smart
Manufacturing" in an automated factory.
Quality
Meeting customer expectations
Efficiency
Improving business performance
Innovation
Continuously creating and innovating
Discipline
Implementing tasks reliably and consistently
AIQ Smart Quality
Self-adjusting control parameters
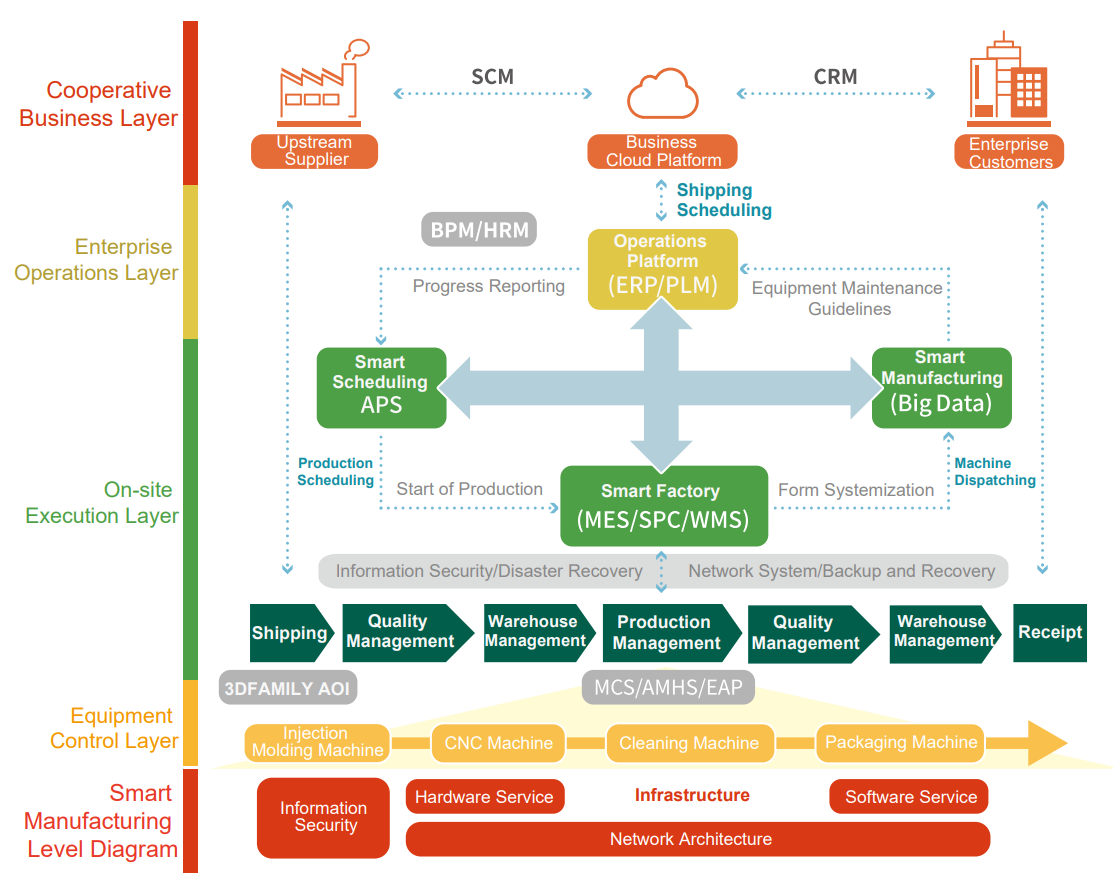
Smart Manufacturing Blueprint
To be a service provider that customers perceive as fast,
high-quality, and safety-oriented.
Strategic Objectives | 2023 Goal | 2023 Achievements and improvement | 2024 Goal |
---|---|---|---|
Customer Satisfaction | Customer satisfaction reaches 85 points | Exceed the target, reaching 94 points | Customer satisfaction reaches 85 points |
On-Time Delivery Rate | Target of 95% | Exceeded the target at 96.50% | After handling customer complaints, issue satisfaction surveys to achieve a satisfaction score of 80 points |
Product Complaints | Target of less than 6 cases | Exceeded the target with more than 6 cases, promptly identifying the reasons and providing corrective measures through an 8D Report to prevent recurrence | Target of less than 6 cases |
Listening to each customer's voice is essential to truly understand their actual requirements. Based on customer feedback, Gudeng takes a responsible approach to address customer concerns, with dedicated teams responsible for handling complaints and analyzing and improving on-time delivery rates and product complaints. This ensures our commitment to customer satisfaction.
Gudeng Precision also proactively implements the 4p4c policy to maintain customer partnerships, even actively identifying yield issues in customers' processes in the PCB industry, providing solutions for large-size carriers to enhance customer process yields and explore new blue ocean markets.
To proactively capture potential future customers and gather market intelligence, we design educational training courses to train our sales team. The training content and goals are updated annually, ensuring all team members are knowledgeable about the industry and new products. We conduct work-sharing sessions and introduce key customers, while also engaging in regular newspaper, magazine, and professional journal coverage. We conduct regular customer visits, participate in international semiconductor and mask industry exhibitions, and collaborate with the SEMI Association.
Through these efforts, we successfully developed revenue from 34 new customers in 2022.
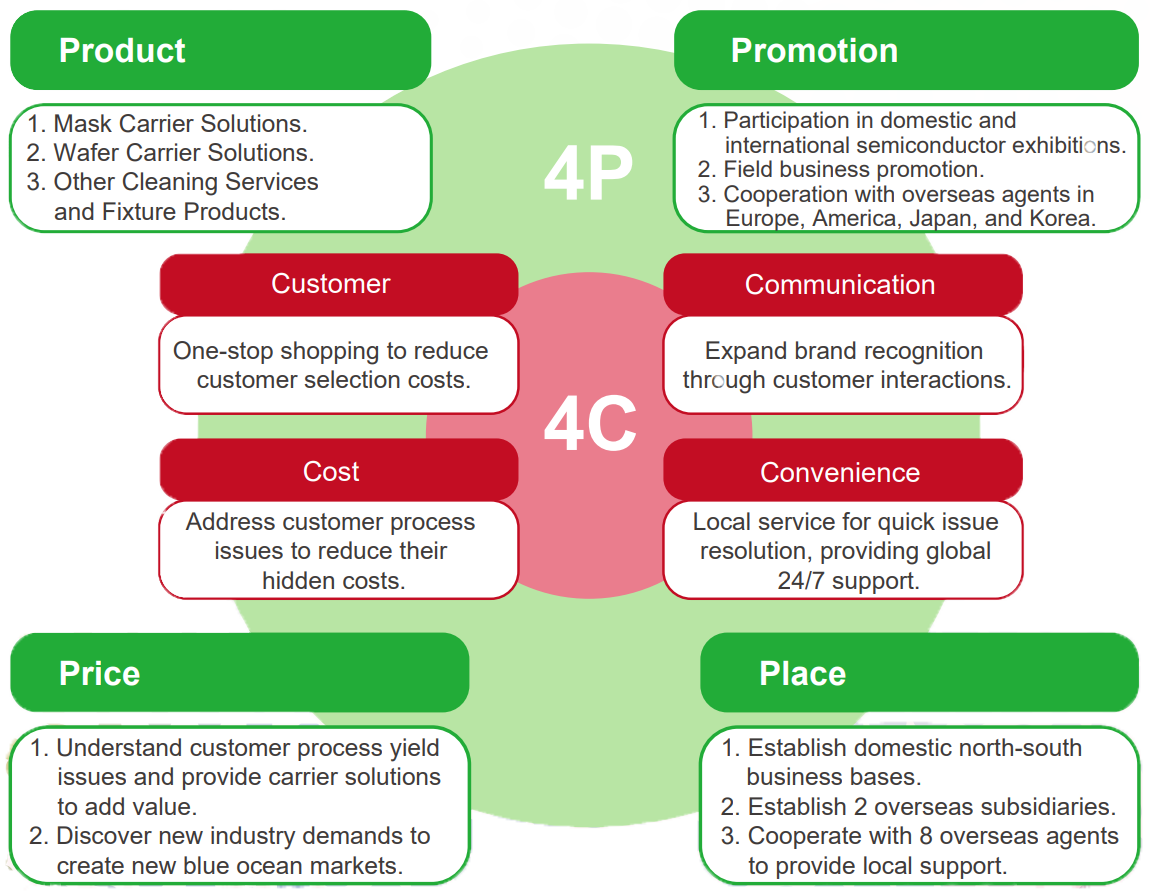
Customer Satisfaction
Gudeng Precision regularly sends questionnaires to customers at the end of each year to
conduct satisfaction surveys with key stakeholders. Customer satisfaction is quantified
using scale patterns, and the results are fed back to internal departments such as sales,
R&D, and quality control for subsequent monitoring and to set the benchmark for improving
customer satisfaction in the future.
In 2022, a total of 22 questionnaires were issued
based on the top 10 key customers and revenue proportion principles,
with 21 responses received, resulting in a response rate of 95%.
Key customers rated overall service satisfaction
related to quality, technology, and on-time delivery at 94 points.
Customer Satisfaction Survey
Average Customer Satisfaction | Quality | Delivery | Service | Technique | Overall Satisfaction |
---|---|---|---|---|---|
Score | 9.56 | 9.29 | 9.4 | 9.33 | 9.4 |
Satisfaction (%) | 96% | 93% | 94% | 93% | 94% |
Customer Satisfaction
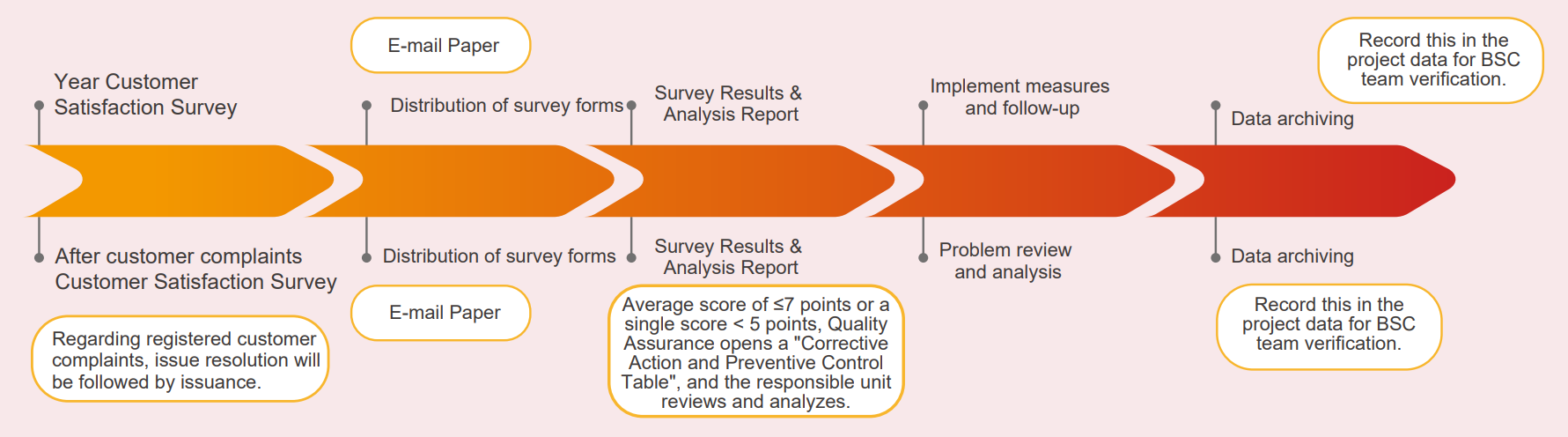
Customer Complaint Handling Process
- The Sales Team must contact the customer within 24 hours to confirm the actual issue and complete the Customer Complaint Consultation Form to be transmitted to the Quality Assurance Team.
- The Quality Assurance Team receives the Customer Complaint Consultation Form and tracks the handling progress of the responsible unit, confirming the final report of accountability and saving the data to prevent future occurrences.
- The Shipping Plant Team must provide an emergency measure response to the Quality Assurance Team within 24 hours. Before the responsible unit is determined, the shipping plant provides a report for Quality Assurance to confirm.
- The responsible unit must provide an emergency measure within 24 hours and provide emergency measure information within 48 hours.
- Within 6 working days, cross-unit integration provides Quality Assurance confirmation and, on the 7th working day, provides the final repor t of Quality Assurance confirmation to the Sales Team.
1. Respond to customers promptly within 24 hours
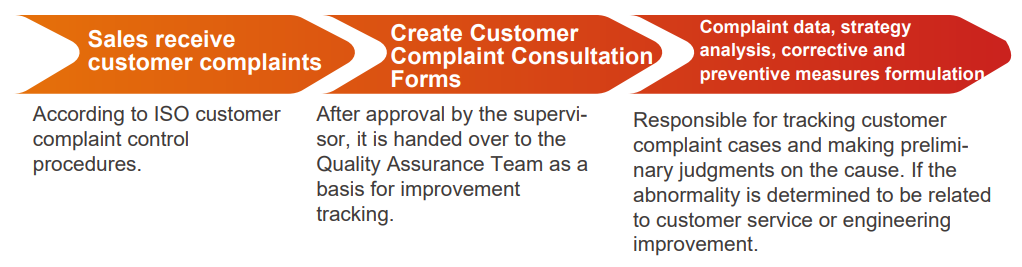
2. Start response process
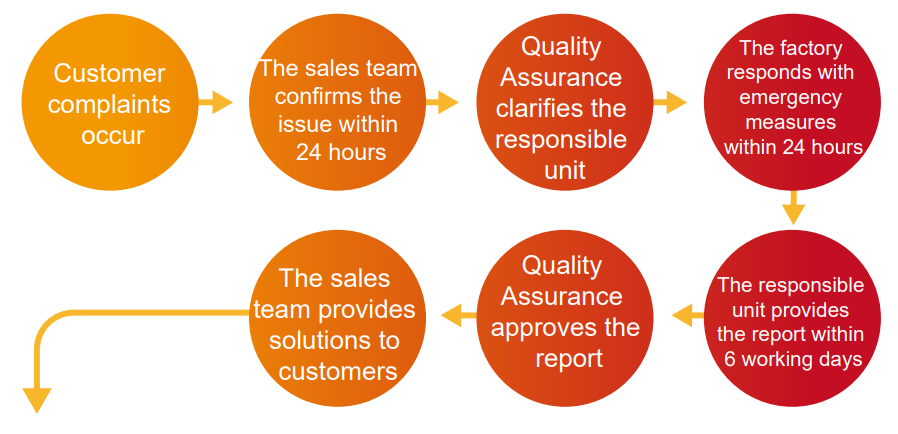
3. After the business provides a solution, continue
to follow up
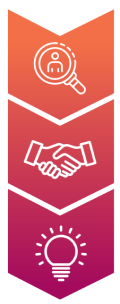
(1) Regularly track product improvement feedback from
customers.
(2) Understand customer needs for future product designs to
optimize
each product shipped in the future.
(3) Simultaneously optimize product design and inspect
production
anomalies.